Финишировал новый проект обучения и развития руководителей производственных предприятий в формате AMP RINQ / REFA 4.0
В последние годы компания RINQ активно разрабатывала новые методы анализа производственных процессов, оценки компетенций и обучения руководителей. В итоге родился формат AMP RINQ для обучения сотрудников производственных компаний методам REFA 4.0. Формат, новаторский даже по меркам немецкой федеральной промышленной ассоциации REFA в целом.
Справка
AMP (Advanced Management Program) – это новый формат executive education, программы для руководителей (топ-менеджеров), успешно реализуемый в мире.
REFA (HTTPS://REFA.DE) – консультант номер один в Европе в сфере промышленной эффективности. Компания RINQ (REFA Industry Navigator Quotient, HTTP://RIN-Q.COM) – является представительством REFA на постсоветском пространстве, работает с 2004 года.
Главная задача, ради которой создавался формат AMP RINQ / REFA 4.0 – выращивание на предприятии руководителей и специалистов экспертного уровня, способных решать самые сложные задачи развития предприятия.
Команды таких внутренних экспертов способны обеспечивать рост производства без наращивания производственных мощностей, превращать «узкие места» в точки роста, выстраивать конвейер по разработке прорывных продуктов и услуг, выходить на перспективные рынки в жестком конкурентом окружении и т.д..
Впрочем, давайте послушаем отзывы из первых уст.
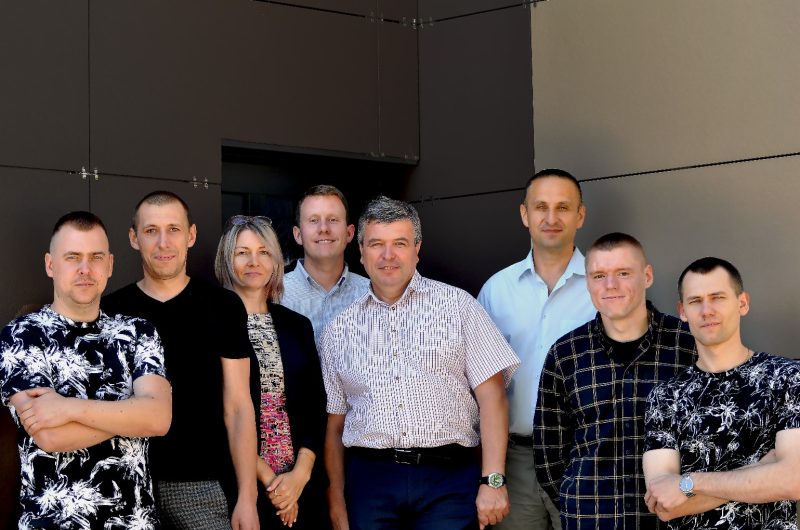
I. «Взглянув под новым углом на привычную проблему, вы увидите за ней новые возможности»
На днях завершилась программа для персонала машиностроительных предприятий «REFA – Оптимизация производства». Мы попросили ее участников поделиться свежими впечатлениями, рассказать, что им особенно запомнилось в программе, что вдохновило, какие инструменты и методы они собираются внедрять на своем предприятии.

Начальник производства ОАО «Управляющая компания холдинга «Лидсельмаш» Александр Жамойдь:
– Я 13 лет занимался производством, считал себя опытным и продвинутым специалистом. И только на программе RINQ понял, как много еще не знаю.
Особенно зацепила идея, которую постоянно напоминали преподаватели: столкнулся с проблемой – не спеши. Отойди в сторону, подумай, постарайся взглянуть на проблему в другом ракурсе.
Вот пример. У нас есть обособленный участок, отгороженный от основного производства стеной. Между ее верхним краем и потолком есть проем, через который с помощью крана передаются на участок детали для обработки. Неудобно? Конечно! Однако все к этому давно привыкли.
Но, стоило увидеть в этом проблему – тут же нашлось и решение. За полчаса мы прорезали автогеном отверстие в стене – и процесс передачи деталей многократно упростился и ускорился. Можно сказать, подход RINQ буквально «пробивает стены».
Другой пример. Сегодня процессы заготовки, сборки и сварки различных изделий у нас происходят в разных производственных корпусах. Много времени и ресурсов уходит на внутрипроизводственную логистику. Поэтому мы решили собрать связанные процессы в одном месте. В ближайшее время займемся перестановкой оборудования.
Мне раньше приходилось учиться на онлайн-курсах других компаний. Честно говоря, у онлайн формата – очень низкая энергетика и возможности для общения с коллегами и преподавателями. Поэтому меня сильно впечатлил очный формат программы RINQ.
Подача материала у Дмитрия Бенько и других экспертов RINQ – просто великолепные. Чувствовалось, что у них за плечами не только современные методики REFA, но и большой личный производственный опыт. Поэтому мы говорили на одном языке.
Было удобно, что занятия проводились в выходные дни: звонки с работы приходили только в пятницу, а в выходные уже никто не беспокоил. Атмосфера на занятиях была очень комфортная. А занятия и кофе-паузы были спланированы так, что лично я совсем не уставал – хотя работал и учился без выходных.
Начальник производства компании «Арлекс» Дмитрий Дроздовский
– Главное, чему я научился в ходе программы RINQ – находить и расшивать «узкие места» там, где их никто не замечает.
В ходе проекта мы записывали на видео и анализировали рабочие операции. Я научился правильно вести их хронометраж, различать разные виды рабочего времени, находить резервы его экономии. Смотришь итоговые цифры и понимаешь: на самом деле, этот работник на этой операции и не нужен. А раньше просто проходил мимо и не замечал, что он постоянно слоняется без дела.
В ходе обучения освоил несколько полезных компьютерных программ, например, GanttPro. Покажу их своим мастерам. Коллегам тоже важно контролировать сроки своих задач, а мне – анализировать эффективность их работы.
Все преподаватели программы давали отличную обратную связь, по первой просьбе высылали нужные таблицы, шаблоны. Каждый из них – эксперт в своем деле. Поэтому в итоге получаешь качественный результат обучения.


Главный сварщик НПО «Пассат» Максим Специан:
– Больше всего пользы приносит решение проблем, которых никто не замечает. Программа RINQ как раз и помогает научиться видеть возможности там, где глаз давно «замылился».
К примеру, раньше мы исходили из того, что на изготовление изделия уходит 8 часов в день, 40 часов в неделю и т.д.. А сейчас – проанализировали конкретные процессы по секундам и подсчитали, сколько времени реально тратится на работу, а сколько – уходит на простои из-за поломок, непродуманные техпроцессы, нерациональные передвижения, перекуры, разговоры по телефону и т.д.. Раньше – игнорировали эти «провалы во времени», а сейчас – можем ими управлять.
Заместитель главного инженера – главный сварщик ОАО «Управляющая компания холдинга «Лидсельмаш» Владимир Вишевский:
– В ходе программы меня особенно впечатлил детальный разбор производственных проблем из реальной практики нашего предприятия. Не менее полезными были кейсы, как подобные проблемы решают мировые лидеры отрасли. На стыке своего и чужого опыта мы и находили решения проблем. Мне кажется, именно такого обучения, привязанного к практике, сильно не хватает выпускникам вузов.
Понравились инструменты визуализации данных, анализа графиков и диаграмм, проведения презентаций. Они сильно ускоряют работу и помогают доносить свои предложения до коллег.
Еще один плюс – организация учебных команд, в которые включались специалисты из разных областей. Это тоже дает панорамный, свежий взгляд на привычные проблемы. Собираюсь внедрять подобный метод командной работы на заводе.
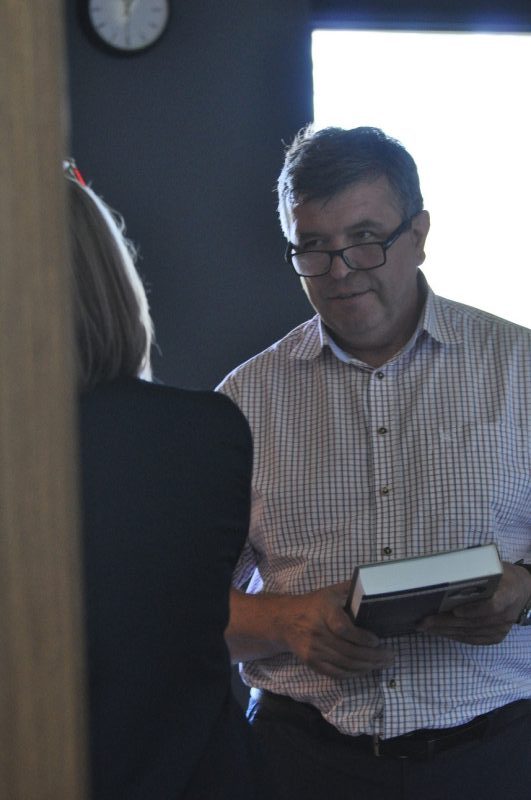

Заместитель начальника производства компании «Арлекс» Олег Донской:
– Все, чему научился, намерен применять на практике. Под моим началом – около 20 рабочих центров. Буду каждый месяц проводить хронометраж их использования, анализировать, сколько времени за смену используется оборудования, корректировать рабочие нормы и процессы. По моим оценкам, это позволит увеличить производительность центров примерно на 30%.
Очень понравилась методика проведения совещаний, с которой нас познакомили на занятиях. На нашем предприятии за смену проводится не менее 4 совещаний. На каждое уходит минут 50. Теперь я понимаю, что время тратилось непродуктивно. Любой вопрос можно решить за 15 минут: поставить задачи, получить обратную связь, сделать выводы.
Еще один полезный навык: техника получения обратной связи от сотрудника. Если вы поставили задачу, а подчиненные закивали головами, это вовсе не значит, что вас поняли правильно. Чтобы избежать проблем в производстве, важно всегда уточнять, что вынес из разговора подчиненный и что собирается предпринять.
Руководитель производственного участка научно-производственного объединения «Пaссат» Константин Александров:
– Эксперты RINQ – отличные мотиваторы и энерджайзеры, умеющие поддерживать веру ученика в свой силы. Помогают друг другу и сами участники программы. Причем, не только во время занятий: мы обменялись контактами и часто созваниваемся.
Очень удачным показался ритм проведения занятий: по три выходных дня раз в три недели. Как раз успеваешь осмыслить полученный материал, применить его на практике, увидеть пробелы в своих знаниях, подготовить вопросы к очередному занятию.
Я уже использую на практике инструменты для хронометража времени и оценки работы персонала, с которыми познакомился на программе «REFA – Оптимизация производства». Теперь я точно представляю, кто и что именно делает за смену на моем участке. Улучшаю процессы планирования и анализа результатов работы с помощью диаграмм разного типа.
Собираюсь внедрять и предложенные на курсе инструменты саморазвития, начиная с обычных календарей и заканчивая специальными таблицами для оценки применения различных навыков. Ведь процесс улучшений бесконечен: решаешь одну проблему – и обнаруживаешь за ней новую проблему и новые возможности.

II. «Мы увидели, как без вложений в оборудование увеличить производство вдвое»
Образовательный проект AMP RINQ получили новый инструмент контроля качества обучения. Каждый участник выбирает прикладной учебный проект и реализует его на собственном предприятии. Защиту проекта принимают международные эксперты RINQ и руководители предприятий-участников программы. Получаем три выгоды за один раз: проверяем полученные знания, запускаем изменения на предприятии, вовлекаем в обучение коллег.
Рассказывают участники программы «REFA: Оптимизация производства».
Александр Жамойдь, ОАО «Управляющая компания холдинга «Лидсельмаш»:
– Рынок сегодня требует реакции в реальном времени. Но, производственная информация на заводе до недавних пор обрабатывалась вручную. Мы уже решаем эту проблему вместе с компанией RINQ. Начали с цифровизации конструкторского бюро. Мой учебный проект тоже с связан с ускорением информационного обмена.
Есть проблема: нашим специалистам приходится параллельно вести до шести и более проектов. Согласитесь, сложно держать в голове критические точки нескольких проектов одновременно и координировать действия с коллегами, не зная, как у них идут дела.
Поэтому я предложил использовать для визуализации проектов диаграмму Ганта.
На большом экране в цехе будет отображаться и постоянно корректироваться информация о начале и завершении различных производственных задач в рамках проектов. Каждый работник сможет наглядно видеть общую картину дел на заводе и понимать, что зависит от него, а что – от коллег. А руководители получат инструмент поиска и анализа причин отклонений от планов.
Я подсчитал, что внедрение диаграммы Ганта за счет лучшего командного взаимодействия минимум позволит вдвое сократить сроки выполнения производственных проектов. Например, если сегодня мы выпускаем зерносушильный комплекс за четыре месяца, то будем выпускать за два. Это даст нам огромную фору по сравнению с конкурентами.
Олег Донской, ООО «Арлекс»:
– Сегодня наша компания наращивает производство торговых и складских стеллажей. Поэтому изначально мой учебный проект был связан с закупкой нового оборудования. По факту, его поставки были отложены на месяц, поэтому я сменил тему проекта на более локальную. Зато новый проект возможно реализовать практически мгновенно.
Речь об оптимизации работы одного из рабочих центров. Он занимает важное место в цепочке производственных процессов, но сегодня стал их «узким местом». На обслуживание центра уходит так много времени, что, фактически, он загружен работой всего 25% времени за смену.
Я предложил совместить переналадку рабочего центра с обеденным перерывом, а его работу – с уборкой и доставкой комплектующих. Одно лишь это увеличит полезное время до 50%.
А после закупки специального штампа мы сократим и количество переналадок. Вложения окупятся всего за три месяца.
Максим Специан, НПО «Пассат»:
– Наше предприятие выпускает технологическое оборудование для горно-химической отрасли. Мой учебный проект связан с зонированием производственных площадей. Выбрал эту тему потому, что на предприятии много времени уходит на поиск деталей и заготовок для рабочих станций. Планируем разделить рабочие площади на участки, присвоить им координаты, отображать в маршрутных картах. Это поможет лучше организовать рабочее пространство, меньше времени тратить на перемещение комплектующих, найти место для дополнительного оборудования и т.д..
В конечном счете, для нас важно не просто сэкономить какие-то средства, а перераспределить время для других, более важных и доходных работ. А еще – работать более ритмично, спокойно и комфортно. Без форс-мажоров, переделок и «тушения пожаров».
Владимир Вишевский, ОАО «Управляющая компания холдинга «Лидсельмаш»:
– Наше предприятие сегодня ищет перспективные ниши на рынке. С этим был связан и мой учебный проект, посвященный развитию производства радиаторов. Сейчас его темпы снижаются. Причины я проанализировал, используя инструменты REFA. А затем разработал план развития производства.
По моим расчетам, предприятие сможет увеличить выпуск определенных моделей радиаторов в два раза. И это без дополнительных затрат на покупку оборудования, только за счет изменения структуры производства и управленческих подходов.
Константин Александров, НПО «Пассат»:
– Сейчас на предприятии остро стоит задача наращивания производства для российских заказчиков. Мой учебный проект помог увидеть резервы рабочего времени на моем производственном участке.
Нередко сварщики и сборщики вместо основной работы вынуждены заниматься комплектацией изделий, переналадкой оборудования и т. д. На это уходит до 5-7% рабочего времени. Я нашел способы сократить эти потери до 3% за счет оптимизации основных и вспомогательных действий работников, хранение комплектующих, инструментов, чертежей. Кроме того, я разработал схему перестановки оборудования, которая освободит пространство для дополнительных рабочих мест.
Эти изменения произойдут в ближайшие два месяца. Рабочие сами ждут перемен. Многие устали от постоянного хаоса: ты наводишь порядок в свою смену – а потом приходит другая смена и перекладывает инструменты по-своему.
Дмитрий Дроздовский, ООО «Арлекс»:
– Нашему предприятию переживает непростые времена. С одной стороны, нужно модернизировать устаревшее оборудование, с другой – погашать кредиты. В своем учебном проекте в рамках программы RINQ я и постарался разрешить это противоречие.
Мой анализ показал: предприятие способно наращивать объемы производства, находить новые рынки сбыта, зарабатывать дополнительные деньги и гасить долги без дополнительных затрат на покупку оборудования. Резервы роста, на самом деле, велики. Нужно лишь правильно организовать хранение материалов, транспортные потоки, работу производственных систем.
Банальный пример. В одном из цехов листовой металл хранился на расстоянии 40 метров от рабочего центра. Почему так сложилось, никто уже не помнит и не задумывается. Но достаточно было переместить металл максимально близко к оборудованию – и процесс подачи материала к месту обработки ускорился в несколько раз.
Учебный проект помог мне переосмыслить собственные стереотипы. Как и любой производственник, я привык оперировать количественными показателями – пресловутыми «штуками». Выяснилось, для предприятия в целом это не всегда выгодно.
Например, есть станок, на котором одновременно работают два специалиста. Я подсчитал, что если оставить только одного рабочего, он произведет за смену на 30% меньше изделий. Зато на 30% сократится себестоимость каждого изделия. А это значит, что предприятие получит от продажи каждого изделия на те же 30% больше прибыли.
Комментирует Генеральный директор представительства REFA Russische Föderation «RINQ» Дмитрий Бенько:
– RINQ вложила в новый проект AMP RINQ весь свой опыт. Причем, не только образовательный, но и производственный. Наш подход – на протяжении всего проекта изменений на предприятии находиться в его цехах и делать результат вместе с заказчиком. Поэтому мы хорошо представляем, как добиться, чтобы знания и навыки конвертировались в нужный результат.
При разработке формата AMP RINQ для обучения производственных компаний методам REFA 4.0 мы определили 9 его ключевых отличий от аналогичных программ:
- Высокая вовлеченность в обучение благодаря актуальной программе, привязанной к реальным потребностям предприятий.
- Глубокое погружение участников вследствие отраслевого характера семинаров.
- Синергия взаимодействия представителей разных производственных профессий за счет продуманной комплектации учебных команд.
- Включение в контекст мирового опыта благодаря большому пакету новейших методических материалов REFA 4.0 в качественном переводе на русский язык.
- Гарантированные инсайты благодаря обязательной видеофиксации реальных производственных процессов и их разбору с помощью методов REFA 4.0.
- Оптимальный баланс между обучением, осмыслением новых знаний, освоением новых навыков и их применением на своем предприятии благодаря продуманному графику учебных сессий (пятница-суббота-воскресенье раз в месяц).
- Надежная поддержка – практические консультации и обратная связь в режимах оффлайн и онлайн от преподавателей, каждый из которых сочетает соответствие стандартам REFA-тренера с богатым личным производственным опытом.
- Удобное расположение нового кампуса в промышленном районе Минске, на минимальном удалении от ведущих производственных предприятий.
- Эффективный контроль обучения + максимальная мотивация обучаемых. Этот двойной результат обеспечивает обязательная защита проекта, реализованного каждым участником на собственном производстве. Экзаменаторы – международные эксперты RINQ и руководители предприятий.

Проект обучения и развития руководителей производственных предприятий в формате AMP RINQ показал: методология REFA отлично работает в белорусском машиностроении, предприятия получили пользу, руководители усилили управленческие и производственные компетенции, благодаря чему предприятия получили рост производительности и качественное решение текущих задач.
Практический опыт RINQ подтверждает, что типология задач REFA позволяет находить уникальные решения для улучшения производственных процессов. Каждый сентябрь стартует набор для новых слушателей и новых проектов. Получить подробную информацию можно уже сейчас, отправив запрос на SEMINAR@RIN-Q.COM.